HD현대 조선 부문 계열사들은 2030년까지 '지능형 자율 운영 조선소'를 구축한다는 방침이다. 이를 통해 생산성 30% 향상, 공기 30% 단축 목표를 달성할 계획이다.
2021년부터 지난해까지 1단계에 해당하는 '눈에 보이는 조선소'을 추진했다. 현재는 2단계 '연결-예측 최적화된 조선소'를 구축하고 있다.
'눈에 보이는 조선소'는 디지털 트윈을 활용한 가상 조선소 '트윈포스'를 수립하는 게 핵심이다. 트윈포스는 가상의 공간에 현실의 조선소를 3D모델로 구현한 디지털 플랫폼으로 직원들은 조선소 현장의 정보들을 디지털 데이터로 한눈에 확인할 수 있다.
트윈포스 구축에 따라 작업자가 건조공정의 상황과 정보를 실시간으로 확인할 수 있어 대기시간 절감, 중복업무 감소 등 업무 효율성을 높일 수 있게 됐다는 게 회사의 설명이다.
HD현대는 선박 건조 전 공정에 디지털 작업지시 시스템을 구축했다. 대형 크레인, 트랜스포터, 지게차 등 주요 설비 및 수송 장비 통합 모니터링 시스템도 구축해 설비 및 장비의 위치와 움직임 등 운용현황을 실시간으로 확인할 수 있도록 했다. 이를 공정관리와 연계해 효율성을 높이고 있다.
'스마트 조선소'의 완성도를 높이기 위해 글로벌 기업들과의 협력도 진행 중이다. 미국 팔란티어 테크놀로지스와 '빅 데이터 플랫폼 구축 및 합작사 설립을 위한 양해각서'를 체결했으며, 독일 지멘스(SIEMENS)와 '설계-생산 일관화 제조혁신 플랫폼 공동개발을 위한 업무협약'도 진행했다.
한화오션은 2021년 스마트 야드 구축을 위해 '디지털 생산센터'를 출범했다. 건조 중인 블록 위치와 생산 공정 정보 현황 등을 드론과 사물인터넷(IoT) 센서 등으로 실시간 확인할 수 있는 '스마트 생산관리센터', 바다 위에서 시운전 중인 선박 상태를 육지에서 확인하는 '스마트 시운전센터' 등 2개의 센터로 구성되어 있다.
한화오션 스마트 생산관리센터는 대형 스크린을 통해 수시로 업데이트되는 각종 생산 정보를 확인하고, 문제가 발생하면 즉시 해결책을 찾을 수 있다. 기상 상황 등 생산에 영향을 주는 불확실성을 예측할 뿐 아니라 시뮬레이션으로 위험 요소를 사전 대응하는 것도 가능하다.
스마트 생산관리센터는 조선사 중 처음으로 드론을 이용한 생산 현장 실시간 모니터링을 시작한 곳이다. 이를 통해 블록과 생산 설비, 장애물 등의 길이와 면적을 자동으로 계산해 활용 가능한 적치 공간을 찾아내고 있다.
또한 현장 전체 상황을 종합적으로 분석해 트랜스포터가 블록을 운반하는 데 필요한 최적 이동 경로를 제시해 공기 단축과 안전성 확보에도 기여하고 있다.
삼성중공업은 지난해 업계 최초로 견적부터 제품 인도까지 선박 건조 모든 과정(EPC)에서 생성되는 모든 정보를 사물인터넷과 AI를 통해 한눈에 확인하고 컨트롤 할 수 있는 데이터 기반 '전사 통합모니터링 시스템'(SYARD)을 개발했다.
SYARD를 통해 데이터에 기반을 둔 최적의 의사 결정이 가능해 인력, 자재, 에너지 등 경영 자원의 효율적 관리, 리드타임 단축, 위험 요인 사전 파악 및 제거가 가능하다. 관리 효율이 강화되면, 인력 부족 개선에도 기여할 전망이다.
업계 관계자는 "조선사들이 첨단 기술 개발에 매진하는 것은 어제오늘 일이 아니다"라며 "한국이 세계 1위 조선 강국 지위를 유지할 수 있도록 연구개발을 지속할 것"이라고 밝혔다.
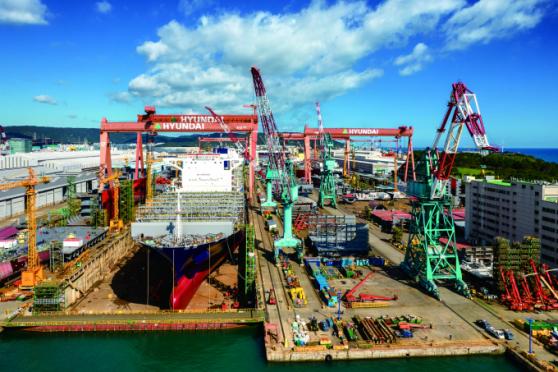